
Choosing a Hardwood Floor

The Fix
How Hard Can It Be to Choose a Hardwood Floor?
Harder than you might think, given all the options available. Here’s how to navigate the various decisions you’ll have to make.

By Tim McKeough
January 7, 2020

In a farmhouse in Duchess County, N.Y., Larson Architecture Works installed reclaimed heart-pine flooring from the Hudson Company. Credit: William Cole.
If you have flooring you don’t like — whether it’s carpet, vinyl or unappealing wood — it can feel like there’s no way to escape it, no matter how many rugs you pile on top. But if you have floors you love, walking across them can be a daily pleasure.
​
That’s because the floor is the base upon which all other decorating decisions are built. Change your floors, and you change the character of your home. It’s as simple as that.
​
So it’s no surprise that new floors — specifically, hardwood floors — are at the top of many renovation wish lists. Not all wood floors, however, are equally appealing or appropriate for every space.
​
“We look at a building holistically, so the walls and windows, and the environment that we’re in, all feed into the decision-making about the floors,” said Paul Bertelli, the design principal of JLF Architects in Bozeman, Mont., whose firm chooses a different wood floor for almost every project.

For the kitchen of a modern house in Dallas, M Gooden Design chose eight-inch-wide white-oak flooring from Carlisle Wide Plank Floors. Credit: Courtesy Carlisle Wide Plank Floors.
The wood flooring industry has evolved considerably in recent years, as wider planks have increased in popularity and finish and installation options have expanded. Given all the choices now available, we asked architects and flooring professionals for advice on how to pick the right one.
Choose the Wood Species and Color
Browsing through flooring samples to choose a type of wood and a color for your new floor is probably the most enjoyable part of the process. At this stage, much depends on personal preference and your overall vision for your home.
​
One of the most popular species is white oak, a classic, durable and widely available wood. “It can also take stain very well,” said Chris Sy, the president of Carlisle Wide Plank Floors. That means it can be customized for a wide variety of aesthetics, from bleached off-white to ebony.
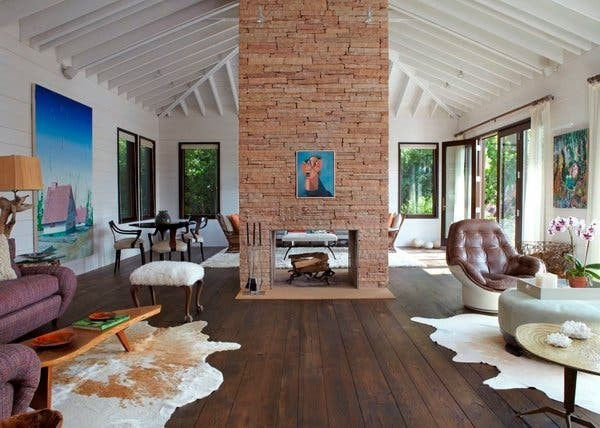
In a Hamptons living room, Fox-Nahem Associates installed reclaimed oak flooring in varying widths from Carlisle Wide Plank Floors. Credit: Courtesy Carlisle Wide Plank Floors.
Other types of wood offer different looks. “Hickory has a lot of color variation, from light tones to dark tones,” Mr. Sy said.
​
Those who want a rich, darker brown usually select walnut, while those who prefer blonder wood may opt for maple or birch.
​
As for choosing a stain, the current trend is toward subtle colors that leave the wood with a natural look. Some designers even eschew stain altogether.
​
“We don’t ever recommend staining floors,” said Elizabeth Roberts, an architect in Brooklyn, though she does occasionally use oak darkened by a process called fuming.
​
If you’re having trouble deciding which species and color is best for your home, consider the other wood elements in the room, Mr. Bertelli suggested. If you have walnut cabinetry, for instance, a walnut floor is an easy match; if you have oak doors, oak floors are a natural choice.
​
“Limit the palette,” he said, “to make it more tranquil and serene.”
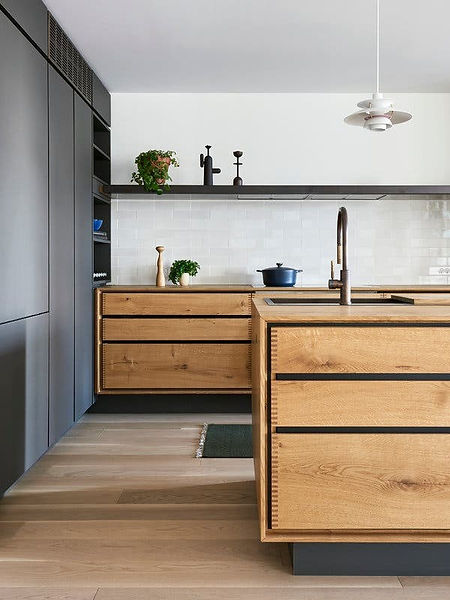
Elizabeth Roberts, an architect based in Brooklyn, N.Y., installed natural-looking white-oak flooring from the Hudson Company in the kitchen of a TriBeCa home. Credit: Kyle Knodell
Consider Wood Grain Character
The way that logs are sawed into boards has a big effect on the grain pattern that’s visible in the floor. With flat-sawn (or plain-sawn) boards, the grain has a wavy appearance. “The defining feature is this arching ‘cathedral,’” said Jamie Hammel, using the industry name for the pattern.
​
Mr. Hammel, the owner of the Hudson Company, a supplier of wood flooring and paneling, noted that quarter-sawn boards offer a more linear appearance, with faint striping: “The prized feature are these medullary rays, which some people call tiger stripes.” Rift-sawn boards offer the straightest, cleanest grain, whereas live-sawn boards may include all types of grain patterns.
​
A floor can use one cut exclusively or can incorporate various types of cuts. A mix of quarter- and rift-sawn boards, for instance, is a popular option for flooring with understated grain patterns. For a warm, woodsy appearance, using only flat-sawn boards might be the best option.

Prefinished boards typically have slightly beveled edges, which create pronounced lines between the boards, as seen in the interior of a Brooklyn townhouse that Ms. Roberts designed.Credit: Dustin Aksland.
In addition to the way the wood is cut, you can choose how many knots and other distinguishing marks you want to see.
​
“We call it character,” Mr. Hammel said, noting that options include “clear” (no knots), “light character” (a few smaller knots) and “character-grade” (the most, and largest, knots).
​
Reclaimed wood is another option. Many flooring companies offer wood salvaged from barns, factories and other structures, which can have even more character — with nail holes, cracks and saw-blade marks.
​
“You can find oak siding off a 150-year-old building that’s been weathered beautifully and use that for flooring,” Mr. Bertelli said, adding that his firm frequently does just that. “We want character in the floor, and our philosophy is that there are perfect imperfections.”
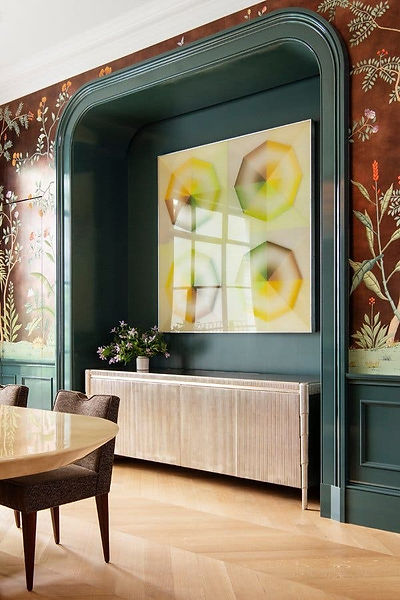
Floors that are finished on site — like this chevron-patterned one in a townhouse designed by Ms. Roberts — give the appearance of a solid plane, without gaps. Credit: Dustin Aksland.
Prefinished or Site-Finished
Another major decision is whether to buy prefinished flooring, sold with its final color and topcoat in place, or unfinished flooring that can be stained and finished by an installer after it’s put down. One of the advantages of prefinished flooring is that it can be installed very quickly, usually in a single day.
​
When floors are finished on site, the home has to be vacated to allow for sanding, staining and finishing, including drying time.
​
“It’s very messy work, and it’s very important that nobody step on it for days, or weeks, at a time,” Ms. Roberts said. “It really alters the construction schedule.”
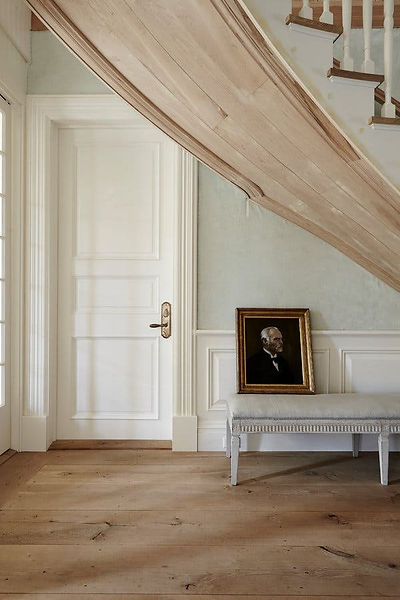
A house by Di Biase Filkoff Architects in Millbrook, N.Y., features live-sawn white oak floors with plenty of character, from the Hudson Company.Credit: Gentl and Hyers.
Because prefinished flooring is made in a factory, companies can also produce it with a wide range of exotic finishes that might be difficult for an installer to recreate on-site and with great consistency.
​
“You know what you’re going to get,” said Jane Kim, an architect in New York. Some installers who do their own finishing, she noted, “may not have the experience to get the color you want, especially if you want shades of gray or a really pale finish.”
​
A key difference, however, is that prefinished boards usually have beveled edges to allow for slight irregularities, which creates more pronounced lines between the boards after installation.
Because unfinished flooring is sanded flat after it is installed, the finished floor typically looks more like a solid plane, without gaps.
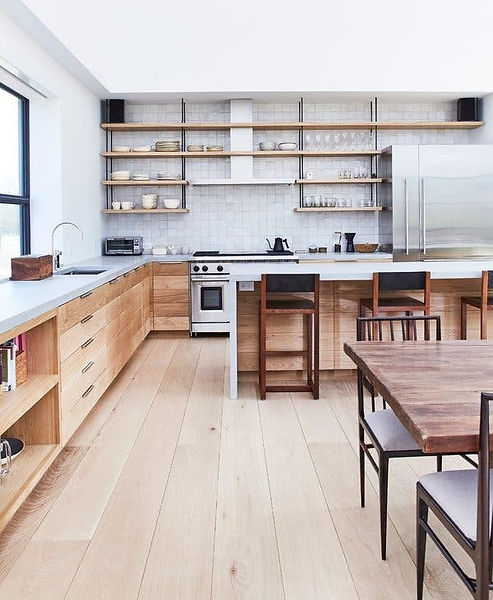
A house by Roger Ferris and Partners in Bridgehampton, N.Y., has flat-sawn white oak floors from the Hudson Company. Credit: Gentl and Hyers.
Choose the Finish
Most hardwood floors today have a finishing coat of clear polyurethane. “Polyurethane essentially sits on top of the wood,” protecting it from moisture, wear and staining, Mr. Hammel said.
​
Water-based polyurethanes have grown in popularity in recent years, and the finishing sheen can range from matte to glossy.
​
A polyurethane finish is very durable, but once damaged or worn, it can be difficult to repair, Mr. Hammel said, because it typically requires refinishing an entire board, if not the whole floor.
An alternative is an oil-based finish. “Oil penetrates into the wood and therefore tends to make it look a bit richer,” he said. And because it doesn’t leave a film on top of the wood, it allows for relatively easy spot repairs.
​
The downside to an oil finish is that it requires more regular maintenance. “An oil floor will dry out over time,” Mr. Hammel said. “But it can be easily refreshed, with more oil.”
Select Solid Or Engineered Wood
Solid wood is just what it sounds like: a plank of your chosen wood, cut from a log. An engineered wood floor is composed of a thinner layer of your chosen wood on top of a manufactured base of layered wood, like plywood.
​
Engineered wood has a number of benefits. “It’s built to be more dimensionally stable,” Mr. Hammel said. “It will expand and contract less,” reducing the chance that the boards will warp or shrink over time. Engineered flooring is especially good in basements, in high humidity areas and over radiant heating systems, he said.
​
And in homes with concrete subfloors, like many high-rise apartments, engineered flooring can be glued directly to the slab, whereas solid wood usually requires a plywood subfloor so it can be nailed in place.
If your ceiling height is low, saving that extra bit of space by using engineered flooring can be important, Ms. Kim said: “Some clients are really obsessed with getting the highest ceiling possible, so if they can save an inch on the floor, they’re going to go with engineered flooring.”
​
But it isn’t always the best option. Some people simply like the idea of solid hardwood better, and in extremely dry areas, solid wood may perform better.
​
“Engineered floors are made to work best in environments that stay above 30 percent relative humidity,” Mr. Sy said. “If the environment is going to be consistently below that, engineered floors may experience slight cracking in the wear layer.”
​
Also, depending on the thickness of that top layer, engineered floors may allow for sanding and refinishing only once or twice — or perhaps not at all — while solid wood can be refinished many times. (To avoid this limitation when buying engineered flooring, look for a product with a thick top layer).
Pick Plank Widths and Installation Patterns
Narrow boards with widths of about two to three inches were once standard for hardwood flooring. Not anymore. Five- to eight-inch widths are now commonplace, and some homeowners opt to go even wider, with broad planks measuring up to a foot wide and beyond.
​
“We make floors up to 20 inches wide,” Mr. Sy said.
​
In general, the wider the boards, the higher the cost. And “the wider it gets, the less stable it gets, because the wood wants to move,” Ms. Roberts said. “When we get into really wide flooring, we almost always recommend an engineered floor, because that prevents it from cupping and warping.”
​
Most floors are installed with the boards in straight lines, but there are many alternative installation patterns, including herringbone and chevron, which are enjoying renewed popularity.
​
More complicated installation patterns also tend to increase the overall cost of the floor, as they require additional labor for installation and result in more wasted wood from the multitude of cuts.
​
How do you decide which board width and installation pattern is best? Consider the proportions of your space, and the style you want: Bigger rooms tend to look better with wider boards, and a herringbone or chevron pattern adds a touch of tradition.
​
You can also mix it up. Ms. Roberts sometimes uses wider boards and complicated installation patterns in the primary living spaces, and narrower boards in a straightforward arrangement in secondary spaces, like hallways and bedrooms.
​
This approach has been favored for centuries as a way to save money, but it can also prevent extravagant flooring choices from overpowering smaller rooms. Remember, Ms. Roberts said, the goal is to create something timeless — not to make “your entire home look like it’s three boards wide.”